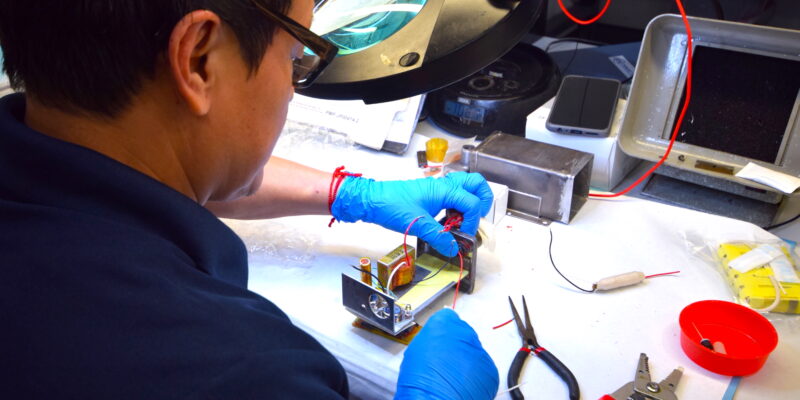
If planes aren’t flying, they’re not making money. It’s that simple. Making matters worse, when regional airlines, private jet operators, or corporations have a plane that’s AOG (aircraft on the ground), the bills keep piling up for everything from aircraft insurance, lease fees, airport usage fees, plane financing, hangar space rental, employee/crew salaries and more. And, of course, AOG’s trickle-down effects often result in inconvenienced passengers, lost business opportunities, or precious cargo not delivered in a safe and timely manner.
“So, it’s not rocket science to say that getting aircraft out of emergency AOG status is critical,” says Stanley Kowlessar, president, and general manager of Thrust Tech Accessories (TTA), an FAA 145 and EASA Certified repair station provider of MRO services in Fort Lauderdale, FL. “That’s where an experienced, reliable MRO (maintenance, repair and overhaul) services company can be invaluable to airlines or aircraft operators, as any repairs or solutions must be meet all government safety requirements and be done as quickly as possible to help customers get their planes back in the air.”
Unexpected Issues
Obviously, if something goes mechanically wroing on the ground or in the air with a broken part, it is typically discovered at once. But unexpected issues can surface suddenly, often after a required aircraft inspection. For example, the U.S. Federal Aviation Administration (FAA) requires A Checks for every 400 to 600 hours of flying time, while B Checks must be done every six to eight months. Other checks too must be made.
With tens of thousands of small parts on planes, things do go awry at times. Yet the reason for an AOG could be as simple as replacement of a malfunctioning sensor. “But if any aircraft fails to pass an inspection, it’s immediately grounded as a safety precaution,” says Kowlessar. “In that circumstance, it’s imperative for the customer to quickly work with a reputable MRO. For example, TTA can help by working with parts manufacturers to secure a replacement part or tap into its own vast parts inventory.
Starting three years ago, to better assist its customers who needed timely parts deliveries, TTA significantly expanded that parts inventory at its Fort Lauderdale headquarters. It also created and received FAA approval for new DER solutions. And just recently, the MRO services company received FAA approval as a prime MRO-services provider for both primary and secondary Learjet aircraft stab actuators.
What’s the Bottom Line
How much does an AOG cost an aircraft owner or operator? It varies considerably by type of operator, type of aircraft, and size of operation. But one Boeing study focused on large commercial aircraft found that an AOG situation can cost airlines up to $150,000 per hour in lost revenue. A separate 2010 research study conducted by the FAA and the National Center of Excellence for Aviation Operations Research (NEXTOR) also revealed that flight delays were costing airlines an estimated $31 billion.
But whether the AOG aircraft is a big jet or instead a smaller regional aircraft, corporate jet, charter plane, or privately owned aircraft, it’s still a money pit while out of service on the ground. Also problematic are pesky, post-pandemic supply chain issues that have impacted parts availability. Fortunately, parts manufacturers or suppliers reserve some parts specifically for emergency AOG situations. But non-emergency orders often have a lengthier delivery time frame.
Code Blue!
Unfortunately, that’s created a perplexing, much more frequent occurrence within the global aviation industry. Some customers are claiming AOG emergencies, even if that’s not the case. They’re doing so simply to skip the line and receive an expedited delivery. That’s an issue. Just think of it this way. In a hospital, a nurse might declare a “code blue” when a patient is critical and there’s an immediate need for a skilled medical team to save a life. So, what if something of a nonemergency nature negatively interrupts that flow of immediate help, expertise, and resources?
It’s a similar situation in aviation when aircraft owners and operators want the top-most priority attention. “That means that when one or two customers then do pop up with true emergency AOG circumstances, the manufacturers may not be as responsive because nearly every order they’re receiving is now claiming to be an emergency AOG,” says Kowlessar.
“We sincerely hope that industrywide, people won’t ‘cry wolf’ and characterize everything they need as an emergency AOG, just to get faster service,” he says. “That will allow us to continue to maintain our well-established, positive relationships with parts manufacturers so we can assist all our clients should they find themselves in a true AOG emergency.”
Preventive Medicine
So, can a good MRO provider can help minimize the incidence of AOGs by ensuring that the aircraft is properly maintained and serviced on a regular basis. The answer is a resounding yes. AOGs can be prevented by conducting regular inspections, maintenance, and repairs on the aircraft to ensure that it is operating safely and efficiently. This includes performing routine checks on critical systems and components such as engines, landing gear, avionics, and hydraulic systems.
In addition, notes Kowlessar, “A good MRO provider like TTA will have a well-trained and experienced team of technicians who can quickly diagnose and repair any issues that arise, minimizing downtime and getting the aircraft back in the air as quickly as possible.”
Overall, partnering with a reliable MRO provider can help airlines minimize the risk of AOGs and ensure that their aircraft are operating safely and efficiently, reducing the impact on their business, and improving the overall customer experience.